Mobile Scanning: A Quick Guide to Warehouse Management’s Essential Tool
Mobile scanners are quickly becoming essential warehouse tools. Pair them with the right software, and you've got an unbeatable competitive edge.
Competition is fierce in warehouse management, and customers aren’t very forgiving. Your company can lose loyalty quickly if it can’t keep orders straight or ship items on time.
That’s why many businesses have turned to mobile scanning technology. The ability to record data with the swipe of a machine empowers warehouses to work faster and better than ever before.
But, as we both know, a scanner is only as good as its software.
NetSuite offers inventory and warehouse management systems within its enterprise resource planning (ERP) platform. The software integrates seamlessly with many types of mobile scanning hardware. It allows warehouse staff to access real-time information from anywhere, including the office and shop floor.
SuiteDynamics works with NetSuite to customize and implement NetSuite ERP systems, including warehouse and inventory management solutions. Our experts can examine your operations and modify the NetSuite platform to suit your mobile scanning needs.
Read our brief guide on mobile scanning technology and discover how NetSuite can boost its capabilities. Then, schedule a free consultation with our team to discuss your company’s needs and learn how a new system can transform your warehouse into an efficient, profit-making machine.
Key Takeaways
- E-commerce growth is driving warehouse modernization, with online sales expected to reach $6.8 trillion by 2028. This growth has made efficient warehouse operations critical, leading to the widespread adoption of barcode scanning technology (used by 83% of surveyed companies as of 2022).
- Traditional manual warehouse operations face significant challenges, including costly data entry errors (up to $2,000 per day in losses from mis-picks), lack of real-time visibility (45% of companies struggle with this), and slow, error-prone quality control processes.
- Mobile scanning solutions dramatically improve warehouse operations by reducing error rates (from 12% to 3%), enabling real-time inventory updates, and supporting sustainability goals through reduced paper usage and improved accuracy.
- Successful implementation of mobile scanning requires careful consideration of barcode types, hardware selection that can support AI/ML capabilities, and cloud integration with Warehouse Management Systems (WMS) for real-time synchronization.
- NetSuite's WMS integrates with mobile scanning technology to provide immediate inventory updates, real-time warehouse operations tracking, mobile quality control, and comprehensive daily operations access through mobile devices, making it a complete solution for modern warehouse management.
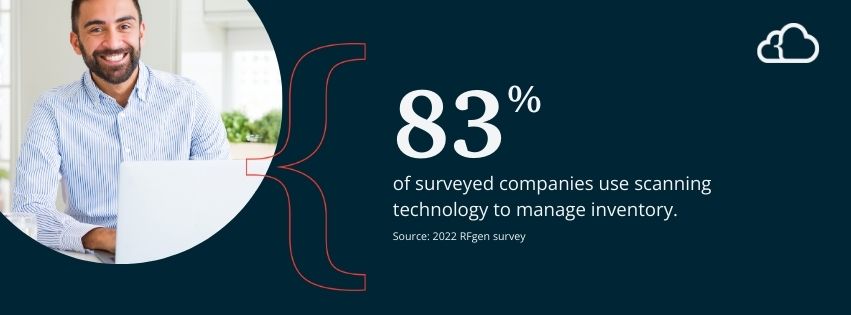
The Evolution of Warehouse Technology
It doesn’t take an analyst to see how much commerce has changed in recent decades. Online retail has been gaining steam, with sales soaring to an impressive $4.4 trillion in 2023. Forrester predicts it will balloon to $6.8 trillion by 2028.
The e-commerce surge has placed enormous pressure on warehouses and fulfillment centers to operate with enhanced efficiency and precision. To cope, more companies are adopting barcode scanning technology to speed up inventory and shipping processes. In fact, a 2022 RFgen survey reports that 83% of respondents use scanning technology to manage inventory.
Consequently, your company needs the best mobile scanning technology to compete.
Primary Challenges in Manual Warehouse Operations
Traditional warehouse management methods face several challenges impacting operational efficiency and bottom-line results.
1. Data Accuracy
Manual inventory management causes data entry errors that affect everything from stock levels to order fulfillment, and those mistakes can be costly. A Peerless Research Group survey found that companies can lose nearly $2,000 per day in revenue from mis-picks.
2. Lack of Real-Time Visibility
Manufacturers need visibility to ensure accurate inventory counts, find the problems causing delays, spot retail trends, identify cost-saving opportunities, and more. However, many struggle to maintain it due to issues like manual processes and insufficient data. According to a study from Standvast Fulfillment and Supply Chain Dive, 45% of surveyed companies cite maintaining real-time visibility across various channels as a chief inventory management obstacle.
3. Quality Control
Traditional inspection methods involve visually examining a product and recording its condition. As with any manual process, this type of inspection takes time and can slow operations, especially when inspectors must check massive amounts of inventory. It’s also prone to human error, compromising overall quality control.
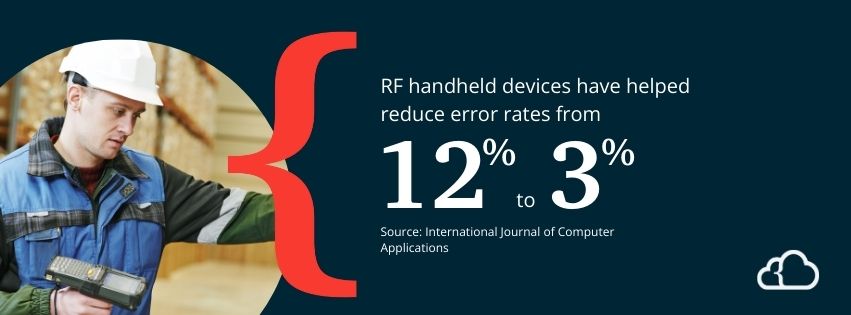
Benefits of Mobile Scanning Solutions
The implementation of mobile scanning technology brings transformative benefits to warehouse operations.
1. Accuracy
Modern scanning solutions improve inventory accuracy through features like force scanning. A force scan ensures correct details, such as lot numbers, serial numbers, and bin locations, are captured before an item is placed in inventory. A study published in the International Journal of Computer Applications (IJCA) reports that RF handheld devices have helped reduce error rates from 12% to 3%.
2. Operational Efficiency
Mobile scanning provides real-time inventory updates, so stock becomes immediately available for subsequent processes like quality assurance, outbound commitment, or fulfillment. Those updates also allow company leaders to track items throughout the manufacturing and order fulfillment process, providing the visibility they need to make informed decisions.
Workers can also use handheld scanners to collect items for multiple orders all at once, increasing picking efficiency while reducing errors through automated validation.
3. Sustainability
Mobile scanning solutions help improve inventory accuracy and decrease paper usage in a warehouse, minimizing waste. These eco-friendly benefits support corporate sustainability goals and often save money.
Implementation Guide
You have to plan carefully and weigh various factors for a successful mobile scanner implementation.
1. Barcode Type
First, select appropriate barcode types based on your product’s characteristics, industry standards, and required scanning distances.
2. Hardware
Next, choose your scanners. Consider your environmental conditions, anticipated scanning volume, and the existing systems that will integrate with your scanners. You also need machines that can support artificial intelligence and machine learning so you can keep up with technological advancements.
3. Cloud Integration
Leading Warehouse Management Systems (WMS) offer real-time synchronization, remote access capabilities, automated backup systems, and predictive analytics that help optimize operations.
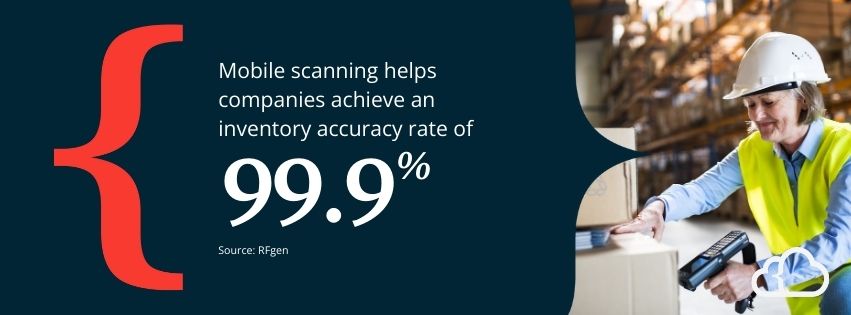
Future of Warehouse Management
There will always be new technologies to change the warehouse management game. At the moment, industry leaders are installing augmented reality picking systems, autonomous mobile robots, IoT sensor integration, and blockchain tracking to set new standards for operational excellence.
These innovations are helping warehouses achieve ambitious performance benchmarks: 99.9% inventory accuracy, 24-hour order fulfillment, zero-error picking goals, and 100% digital tracking. These targets may seem lofty, but they're becoming the standard for competitive operations.
Maintaining Your Mobile Scanning System
You can’t forget about your company’s mobile scanning and expect it to remain successful—no matter how wonderful that may seem. Like all systems, it requires regular maintenance and updates. You have to keep the hardware in good working condition, ensure the software stays current, and offer ongoing staff training. Fortunately, any maintenance your scanning system requires is offset by significant operational improvements and cost savings.
How NetSuite Works with Mobile Scanning Technology
As we’ve stated, mobile scanners work wonders in a warehouse but are useless without a sophisticated software system. NetSuite’s Warehouse Management System (WMS) integrates with mobile scanning hardware, allowing your company to maximize the tool’s many benefits.
1. Immediate Inventory Updates
NetSuite's WMS mobile application updates data in real time so that inventory management delays can become a thing of the past. As soon as a worker scans an item, the inventory records update automatically in the NetSuite system, making the inventory data instantly available for quality assurance, outbound commitment, and fulfillment processes. Consequently, all departments can work with current information.
2. Real-Time Warehouse Operations
NetSuite allows companies to use mobile scanning technology in multiple warehouse functions. Warehouse staff can scan work order components, process complete work orders with associated bills of materials, manage replenishment by scanning items and quantities, and track inventory movements between warehouse locations. The system instantly updates with each scan, maintaining accuracy across operations.
3. Mobile Quality Control
NetSuite's tablet interface tackles quality assurance efficiency. Quality control staff can use the feature to capture and process test results directly from the shop floor or receiving dock, meaning they don’t have to return to a desk to input data. This mobile capability ensures quality checks happen where and when necessary, streamlining the inspection process.
4. Daily Operations Access
The true power of NetSuite's mobile integration lies in its ability to put all daily warehouse functions in the palm of workers' hands. Staff can use the mobile application to access real-time information and perform tasks anywhere in the warehouse. This mobility increases operational efficiency and ensures data remains accurate and current throughout all warehouse processes.
5. System Requirements and Setup
Your warehouse must have compatible scanning devices and a stable wireless connection to implement NetSuite's mobile scanning capabilities. The system works with various types of scanning hardware, from dedicated scanning devices to tablets and smartphones with scanning capabilities. This flexibility allows businesses to choose the best hardware solution for their needs and budget.
Our team will explain more about NetSuite’s mobile scanning features during your free consultation. We’ll also discuss how our experts can modify the software to suit your company’s unique needs so your staff can work smarter and not harder.
Drive Customer Loyalty
Customers won’t stick around after receiving incorrect orders or suffering shipment delays—it’s an unalterable fact of the business world.
That’s why you can’t rely on manual labor for inventory management. Mobile scanning technology, paired with NetSuite warehouse and inventory management solutions, ensures your staff records correct product information and feeds your team the real-time information it needs to perform at its best.
We know how important efficiency and customer satisfaction are to your business. Schedule a free consultation with our team and start transforming your warehouse into a robust operation that drives profits and keeps consumers happy. Together, we’ll watch your company rise in the marketplace.
Frequently Asked Questions
Can NetSuite's mobile scanning capabilities be extended to field operations outside the warehouse?
NetSuite's mobile scanning framework can be extended to field service, delivery verification, remote inventory management, field agent time entry, and on-site customer asset tracking. Field technicians can use the same scanning infrastructure to verify parts installation, capture customer signatures, and automatically trigger billing upon service completion.
This unified approach eliminates data silos between warehouse and field operations, providing true end-to-end visibility. Implementation requires additional configuration and potentially custom development through SuiteScript to accommodate field-specific workflows. Companies typically see the most significant ROI when implementing consistent scanning processes across both warehouse and field operations, as this eliminates manual reconciliation between systems.
What cybersecurity considerations should be addressed when implementing mobile scanning technology integrated with NetSuite?
Key security considerations include:
- Device management policies for scanner loss or theft
- Authentication requirements (biometric vs. password-based access)
- Network security for warehouse WiFi infrastructure
- Data encryption for inventory information in transit
- Access controls limiting which employees can modify inventory data
- Compliance with industry regulations for data handling
- Secure API and third-party connections
Most IT security teams recommend implementing a dedicated VLAN for warehouse scanning devices, regular security audits, and integration with existing identity management systems to maintain a secure environment without compromising operational efficiency.
We pull information from NetSuite material, SuiteDynamics experts, and other reliable sources to compose our blog posts and educational pieces. We ensure they are as accurate as possible at the time of writing. However, software evolves quickly, and although we work to maintain these posts, some details may fall out of date. Contact SuiteDynamics experts for the latest information on NetSuite ERP systems.
Disclosure: This article was developed with the assistance of Claude, an AI created by Anthropic. Our editorial team used Claude as a collaborative writing tool, carefully reviewing, editing, and fact-checking all AI-generated content. The final text has been thoroughly vetted to ensure accuracy, clarity, and alignment with SuiteDynamics' editorial standards. We take full responsibility for the content presented in this article, maintaining our commitment to providing reliable and informative insights to our readers.